Doubling welding wires can more than double production line throughput
Originally popular in submerged arc welding, tandem-wire technologies were extended to the automated gas metal arc welding (GMAW) process in the early nineties.1 Since their introduction, more than 1000 tandem- wire GMAW systems have been installed worldwide, most replacing single-wire systems that had been pushed to the limits of their weld metal deposit rate and productivity range - Fig. 1.
Fig.1 - Tandem-wire GMAW deposition rates compared to single-wire processes.
The tandem-wire GMAW process employs two electrically isolated wire electrodes, one behind the other in the direction of welding - Fig. 2. The first wire electrode is referred to as the "lead electrode" and the second as the "trail electrode." The spacing between the two wires is close enough to enable them both to deliver metal to a single weld pool. The lead electrode generates most of the base metal root penetration, while the trail wire controls the weld pool for bead contour and edge wetting while it adds to the overall deposition rate.

The process works best with a large- diameter lead wire and a small-diameter trail wire. The larger lead wire may represent as much as 65% of the total process deposition rate while providing greater process penetration. Focused on the back edge of the molten weld pool, the trail wire, drawing a lower current, is better able to cool and control the pool. Sometimes wires of equal diameter are specified because of inventory constraints or if the welding direction is reversed somewhere on the weldment, but this compromise limits travel speed and reduces the productivity of the process - Fig. 3.

Tandem-wire GMAW depends on specialized power control software to manage the stable operation of two independent direct current welding arcs working in very close proximity, where disruptive electromagnetic influences would cause severe instability if not precisely regulated.
Fig.4 - Typical configuration of a hard-automated tandem-wire GMAW system.

Equipment ConfigurationIn order to provide individual parameter control for each of two separate, electrically isolated welding arcs, a pairing of equipment is required: two specially designed inverter power sources, two wire drives, and two separate welding wire payoff sources - Fig. 4. The power sources rely on fast digital control and specialized software. Welding parameters are set at the power sources via digital communication from a programmable logic controller associated with a dedicated hard-automation workcell or by a robot controller.

The tandem-wire welding gun (Fig. 5) is a critical component of the system, engineered with specific contact tip alignment and spacing to achieve proper arc control. To withstand high-amperage, high-duty-cycle production runs, welding guns are generally rated at the total current flowing in both electrode wires - typically in the 600- to 1200-A range. The maximum current specified for each wire is typically in the 400- to 800-A range.
Process BenefitsThe tandem-wire GMAW process can dramatically increase travel speed in sheet metal welding, and significantly increase weld metal deposition rates in heavy plate welding. The increased productivity of the tandem-wire GMAW process can improve the profitability of existing automation. In addition, it may justify the cost of new automation equipment since it can reduce the number of weld stations that would otherwise be needed and shorten payback periods associated with investment in welding automation.
Fig.6 - Root filling capabilities on 0.100-in. material at 100 in./min.
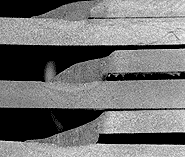
Welding operators involved in thin-gauge metal industries such as automotive, tank, and general sheet fabrication, are traditionally faced with two quality issues - melt-through and lack of metal follow characteristics - when pushing travel speeds to the limit.

Operating at speeds in excess of 100 in./min (with 0.040- to 0.120-in. materials), the tandem-wire GMAW process addresses both of these speed-limiting issues. Distributing the welding current over two wires allows the lead wire to generate the required joint penetration while the trail wire rides on the back edge of the lead weld pool, creating added fill as well as additional force against the weld pool for better follow and wetting characteristics. This riding of the weld pool with the trail arc provides excellent root filling capabilities, especially important to industries processing large numbers of stamped or formed parts - Figs. 6, 7.
Fig.8 - Eight-ft truck bolster plates being joined with tandem-wire GMAW. A 5Ž16-in. fillet weld

In heavy plate fabrication, the tandem-wire GMAW process can represent a 30 to 80% increase in deposition potential compared to single-wire processes - Fig. 1. The tandem-wire process typically employs smaller-diameter (0.035 to 0.062 in.) electrodes. As higher welding currents are applied, the electrode melt-off rate rises geometrically. For a given current draw, the melt-off rate for the tandem-wire process is greater than that of a single wire of larger diameter. This higher melt-off rate leads to higher production throughput, while the lower amperage draw (and lower heat input) reduces plate distortion and cooling time between multipass welds. The process is capable of producing X-ray quality welds with excellent mechanical properties - Fig. 8.
Return on Investment The tandem-wire GMAW process was designed for use in automated welding cells or automated lines. Investment in these high-volume production lines is a capital expenditure that must be cost-justified. Welding-speed-critical floor-to-floor time of parts is an important factor in the equation. Compared to single-wire processes, tandem-wire GMAW's higher travel speed capabilities can help justify greater capital expenditures and accelerate equipment payback periods - Figs. 9, 10.

Tandem-wire GMAW systems can reduce the cost of new production lines by meeting output needs with fewer welding stations. This is particularly true for high-volume production lines producing automotive components or similar parts where tooling and part-handling equipment constitutes a sizeable portion of the initial installation cost. Using fewer welding stations with a higher per-station throughput may reduce the cost of expensive tooling and handling equipment. Additionally, the expenses of upkeep and maintenance time for managing consistent part dimensions coming off of duplicate tooling sets are minimized.
Fig.10 - Production capabilities of single-wire vs. dual-wire GMAW.

Cost-justification for workcells welding large components (for example, earth-moving equipment or offshore drilling rigs) is based more on welding time than part count. These cells utilize capital-intensive positioners to handle large, heavy weldments that can take two or more hours to weld, often in a flat or horizontal position that allows access for only one robot per cell. In order to improve the return on these large cells, overall welding time must be reduced by increasing the weld metal deposition rate. The industry has responded by replacing single-wire robotic systems, with average deposition rates of just 1520 lb/h, with tandem-wire systems operating in the 2834 lb/h range. The increased weld metal deposition rate has been used to justify the cost of purchasing new, more technically sophisticated workstations.
Article by :
TIM MOREHEAD is Product Manager Tandem MIG Process, at The Lincoln Electric Company, Cleveland, Ohio, (216) 481-8100.
No comments:
Post a Comment